Summary
- Streamlined Inventory Management: 10X ERP’s automated replenishment uses intelligent reorder points and real-time data to eliminate stockouts and overstocking, ensuring optimal inventory levels and improved purchasing accuracy.
- Seamless Vendor Integration: The system integrates with vendor management systems to automate purchase orders, optimize lead times, and reduce procurement costs through data-driven vendor selection.
- Enhanced Operational Efficiency: Automated replenishment saves time, improves cash flow, and boosts customer satisfaction by maintaining accurate stock levels and enabling faster, more reliable order fulfillment.
Effective inventory management is vital to a distribution business’s success, as it directly impacts customer satisfaction, cash flow, and operational efficiency. One powerful feature of 10X ERP is automated replenishment, which eliminates the guesswork from stock management and ensures businesses maintain optimal inventory levels at all times. Through automated triggers, real-time data, and intelligent integration with vendor systems, automated replenishment ensures that stock levels stay balanced, reducing the risk of stockouts and overstocking while optimizing purchasing processes.
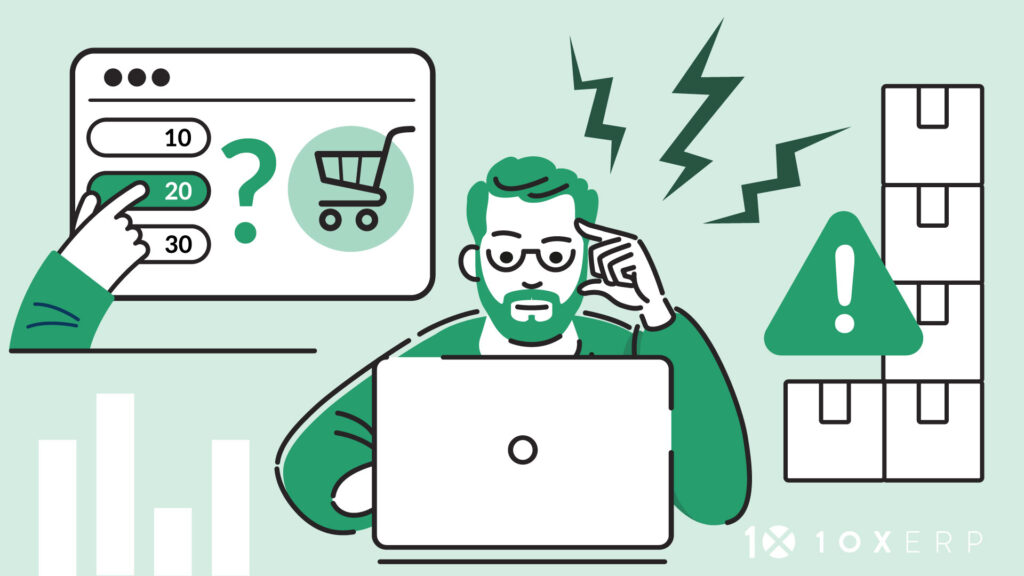
The Problem of Manual Inventory Replenishment
Manual inventory management is prone to errors and inefficiencies, even with some digital support. It often involves staff tracking stock levels through spreadsheets or ERP systems that require frequent updates. Managers must closely monitor sales trends and seasonality to predict when stock needs replenishment. This reactive approach can lead to either over-ordering, which ties up capital and storage space, or under-ordering, resulting in stockouts that disappoint customers and disrupt operations.
Businesses that rely on guesswork or manual monitoring to manage stock often face delays, errors, and missed opportunities. Worse, misjudging inventory needs can lead to costly consequences, such as excess stock that becomes obsolete or missed sales opportunities when products are unavailable.
Automated replenishment eliminates these issues by continuously monitoring inventory levels, setting reorder thresholds, and triggering purchases when necessary—keeping your business running smoothly without manual intervention.
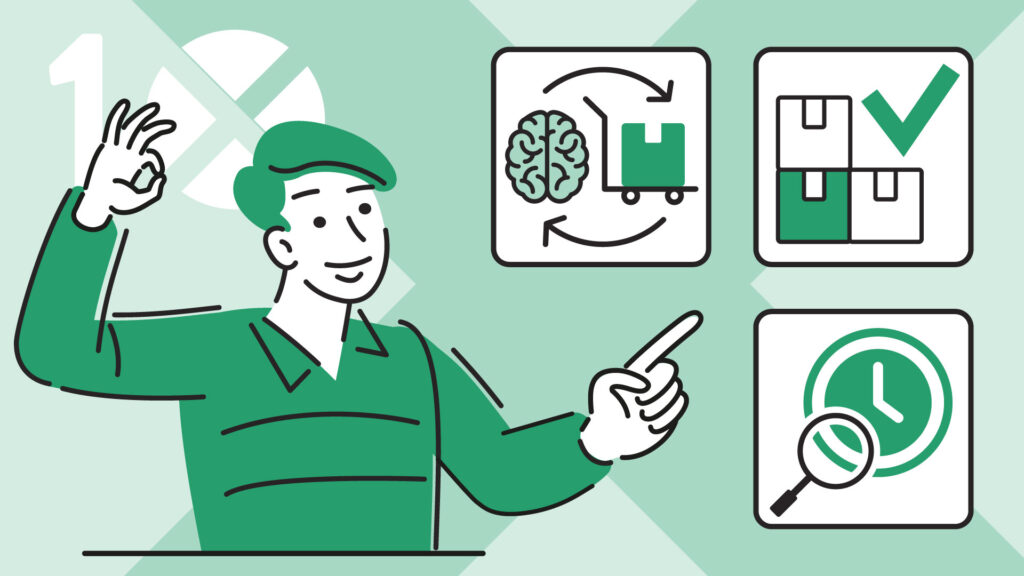
How Automated Replenishment Works in 10X ERP
Intelligent Reorder Points
With automated replenishment, businesses can set up smart reorder points for their inventory based on historical data and future demand forecasts. 10X ERP monitors stock levels in real-time and automatically generates purchase orders when the inventory drops below a specified threshold. These reorder points are tailored to each item, accounting for sales velocity, supplier lead times, and seasonality. As a result, businesses maintain optimal stock levels, ensuring they’re neither overburdened with excess inventory nor understocked during peak demand periods.
Elimination of Stockouts and Overstocking
The system can detect trends and anticipate inventory needs based on actual sales patterns by automating the process. This eliminates the guesswork that typically leads to stockouts or overstocking. Stockouts can lead to missed revenue and damage customer relationships, while overstocking ties up capital and increases storage costs. Automated replenishment ensures that items are available when needed without accumulating excess inventory, striking the perfect balance.
For example, if a popular product is trending upward in sales, 10X ERP’s automated replenishment system adjusts reorder points to ensure there’s enough stock on hand to meet demand. Conversely, the system reduces unnecessary reorders for slow-moving products to avoid surplus.
Real-Time Data and Predictive Analytics
10X ERP’s automated replenishment system uses real-time data to continuously track sales and inventory movements. This dynamic approach allows the system to make better predictions about future stock needs. Additionally, it considers vendor lead times, upcoming promotions, and other factors that could impact inventory requirements.
Predictive analytics also helps identify trends in purchasing behavior or seasonal changes. With this information, the system can adjust reorder levels dynamically to align with anticipated demand. This minimizes the chance of running into stock issues or wasting resources on products that aren’t moving.
Integration with Vendor Management Systems
10X ERP’s automated replenishment doesn’t operate in isolation. It integrates seamlessly with vendor management systems to streamline the purchasing process from start to finish. Here’s how the integration enhances efficiency:
Simplified Purchase Orders
The system can automatically generate and send purchase orders to preferred vendors when a replenishment trigger is activated. The process is fully integrated, meaning the system selects the appropriate vendor based on pricing, lead time, and historical performance. This eliminates manual intervention in the ordering process, saving time and reducing errors.
Vendor Collaboration and Lead Time Optimization
Automated replenishment also facilitates better collaboration with suppliers. Businesses can share data about upcoming stock needs with vendors, making them plan their inventory and production more effectively. Additionally, 10X ERP keeps track of vendor performance, such as lead times and fill rates, so that the system can adjust orders for potential delays.
For instance, if a critical supplier typically takes two weeks to deliver, the system will account for that lead time when determining when to place the order. As a result, businesses are less likely to face unexpected delays, and they can maintain a more consistent inventory flow.
Reducing Costs Through Vendor Comparison
In many cases, multiple suppliers may offer the same products. 10X ERP’s automated system can compare vendor pricing and performance metrics, ensuring businesses get the best possible deal. By analyzing lead times, shipping costs, and pricing, the system can help reduce procurement costs while providing timely goods arrival.
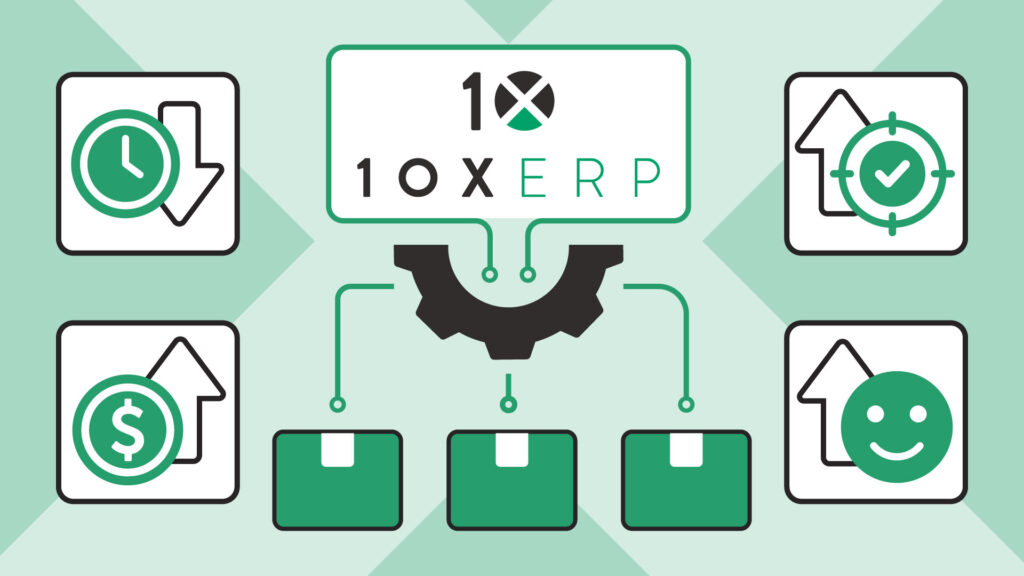
Benefits of Automated Replenishment
The benefits of automated replenishment are significant, particularly for businesses that manage extensive inventories. Here’s how automation drives operational efficiency and improves business outcomes:
Time Savings
One of the most significant advantages of automated replenishment is the time saved by eliminating manual inventory monitoring and purchase order creation. Staff can focus on more strategic tasks while the system handles routine inventory management.
Enhanced Cash Flow
By maintaining optimal stock levels, businesses can reduce the capital tied up in excess inventory. Automated replenishment ensures that items are ordered only when needed, freeing up resources for other parts of the business.
Improved Accuracy
The system’s reliance on real-time data and predictive analytics improves the accuracy of purchasing decisions. Automated replenishment removes the risk of human error from inventory tracking, resulting in more precise order quantities and fewer stock discrepancies.
Increased Customer Satisfaction
The most important benefit of automated replenishment is its positive impact on customer satisfaction. With the right products always in stock, businesses can fulfill orders faster, meet customer demand, and improve overall service levels.
Conclusion
Automated replenishment, as offered by 10X ERP, is a powerful tool for optimizing inventory management. By leveraging real-time data, intelligent reorder points, and seamless vendor integration, businesses can eliminate the inefficiencies of manual stock management. The result is a more efficient supply chain, reduced stockouts, lower carrying costs, and a more profitable and responsive business.